
Тема уже из заголовка ясна: каждый день сталкиваюсь с непониманием того, сколько на самом деле стоит разработка корпуса.
И цель этой заметки рассказать вам о том, сколько действительно придётся за неё заплатить: 100 000 рублей, двести или миллион. Прочитав эту статью, вы сможете определить, сколько придётся отдать за работу и заодно понять, недоговаривают ли вам что-то разработчики по поводу цен или режут суровую правду.
Ответим на три основных вопроса:
Сколько нужно денег на разработку корпуса, почему столько и где можно сэкономить, если очень нужно?
Начну, как всегда, чутка издалека а из чего в принципе складывается цена корпуса? Если кратко, то вот:

Я уже писал на Хабре, как быстро оценить себестоимость
производства корпуса и приводил примеры цен разных корпусов с разными
параметрами. Но нигде и никто не пишет, сколько стоит собственно
разработка корпуса. Вот самое время об этом написать с пруфами,
Билли, примерами и цифрами, как я люблю.
Разработка поэтапно с человеко-часами за каждый этап
ТЗ
О том, из каких этапов состоит разработка корпуса, можно узнать из ещё одной нашей статьи на Хабре. Но это скорее внешняя сторона вопроса, а вот того, что происходит на нашей кухне, не видит никто (хотя процессы схожи с любой разработкой электроники или программированием например, с разработкой платы или софта на неё).

Сначала мы пишем за клиента ТЗ (скоро расскажем, почему сами). Для этого собирается первичная информация в виде опросника (скачать formlab.ru/useful), вытаскивается нужная инфа из разговоров с клиентом и его разработчиками, раскладываются по папкам референсы, модели, документация, и всё это отдается техническому писателю, который за 3-5 дней готовит простое техническое задание (мы его называем дизайнерское ТЗ). Формально там мало ограничений, кроме основных габариты, себестоимость производства, технологии, эргономика и т.д. Вот примеры: formlab.ru/tz.
Начинаем считать.
Технический писатель, составление ТЗ: +20 человеко-часов
Промдизайн
Дальше к работе подключаются промышленные дизайнеры тут все просто. Этот процесс сильно размазан во времени, потому что человеку надо прогреться, т.е. поварить в голове задачу, посмотреть на конкурентов, прикинуть, что вообще можно сделать, и рисовать рисовать рисовать
Средний проект занимает 2-3 недели работы дизайнера. Обычно их на проекте двое. Половина времени тратится на поиск стиля будущего корпуса, а половина на более детальную прорисовку того, что напридумывали.

Хозяйке на заметку: если дизайнер говорит, что все сделает в 3D, потому что сейчас уже никто не рисует, то знайте, что он работает раза в 1,5-2 медленнее, чем дизайнер, который рисует руками. Такой в 3D вам обойдётся вдвое дороже, короче.

дизайнеров смотрят на меня сейчас так, простите, коллеги, но это статистика лет так за десять уже :)
Промышленные дизайнеры, прорисовка эскизов +80 человеко-часов.
Моделирование

Затем корпус надо прорисовать уже в 3D и подготовить визуализацию. Это либо тот же дизайнер, либо отдельный моделлер (у нас отдельный, кстати) и визуализатор (у нас отдельного нет) ещё неделя.
Модель и визуализация дизайна корпуса в 3D +40 часов.

Инжиниринг
А вот дальше начинается самое интересное это инжиниринг корпуса. Абсолютно внутренняя штука, которую заказчик даже и не видит иногда. Но чаще видит, поскольку проходит итерационная работа между конструктором корпуса и разработчиком платы. В общем процесс выглядит так:

При необходимости возвращаемся на прорисовку геометрии и дальше по кругу.
Инжиниринг во всех наших проектах занимает больше времени, чем разработка дизайна. Другого не дано. Простой корпус (о сложности ниже расскажу) это работы на месяц как минимум (а с бумажками два!). Про сроки, кстати, писал вот тут, почему-то нет на Хабре возьму на заметку.
Инжиниринг корпуса, согласование с производством +160 часов.

Прототипирование


Добавим в копилку проекта еще 50 часов на работу конструктора.
50 часов это ещё нижняя планка, когда конструктор и завод просто не то что знают друг друга, а лет эдак 5 работают в тесном контакте.
Хозяйке на заметку если вы считаете, что прототип это только сам прототип, т.е. его физическое изготовление, то ошибаетесь: это куча работы до, во время и после производства. И всё это нередко дороже и сильно дольше непосредственно производства.
Итак, в копилке 350 человеко-часов на простой корпус. Вопрос: сколько же стоит такой человеко-час? Об этом ниже, так как все не так однозначно.
Как оценивать сложность корпуса
Я специально беру в пример простой проект, так как их большинство и мы уже в них собаку съели два из трёх корпусов, которые у нас заказывают, именно простые.
Но есть другая треть, которую уже сходу не оценить. И как понять на берегу, простой корпус или сложный?
Очень просто: оценка сложности проекта это количество деталей + сложность их соединения друг с другом. Представьте, сколько деталей в корпусе вашего устройства: кнопки, стекла и вот это все.
Вот простенькая схема для оценки сложности корпуса по количеству деталей:

Затем решаете: нужны ли деталям какие-то особые соединения? Например, герметичность. Или виброустойчивость. Или гибкость. Или вентиляция платы особенная, а не просто отверстий наделать
Если что-то из вышеперечисленного требуется, ваш корпус почти наверняка (но не всегда) будет сложным. Проблема в том, что физические свойства в виртуальной среде можно только имитировать, и очень условно, но для полноценной проверки (герметичен ли он на самом деле ил нет) потребуются несколько прототипов и куча работы. Поэтому с вероятностью 90% этап прототипирования будет дольше по времени и обойдётся дороже первичной разработки.
Или в корпусе просто много деталей тогда просто количество рутинной работы по их сопряжению превращается в десятки и даже сотни часов разработчика.
Примеры простых корпусов:


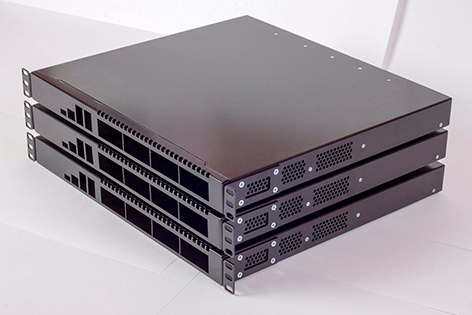
Средние по сложности корпуса:


Сложные корпуса:



Прототипирование часы (минимум-среднее): 50 часов.
Опоздатушки
Вам нужен корпус, вы приходите в компанию разработчиков и они вам обещают, что разработают корпус за месяц. Вы, если опытный боец, уже знаете, что это очень оптимистичная оценка по времени, и закладываете в бюджет 2Х от цены и сроков. Если прям опытный-опытный то 3Х.
Если не очень опытный и верите на слово, через месяц вы видите, что у вас даже еще контракт не согласован, потому что на это есть пара десятков внешне уважительных причин и куча обоюдных тормозов.
Ещё на проект наслаивается такая штука, как ожидания заказчика на этапе заключения договора. Все, кто оказывает сложные услуги, про это знают, но вдруг кто-то нет, рассказываю
Не буду сильно растекаться по древу, почему это происходит, просто кратко если только над проектом работает больше 2х людей, все оценки и прогнозы надо умножать минимум на 2. Я даже как-то статистику составил за 3 года (это примерно 120 проектов), сравнивая время на разработку: то, которое обсуждали в начале проекта и то, сколько он фактически длился.
Так вот, все проекты, даже так ВСЕ проекты заняли минимум вдвое больше времени, чем планировалось изначально. А есть проекты, которые съели человеко-часов и втрое больше, и впятеро. Поэтому ещё пара советов.
-
Не считай, что твои внутренние процессы не задерживают разработчика вы одинаково тормозите друг друга.
-
Не меняй в ТЗ ничего. Если есть хоть какая-то вероятность замены, например, компонента, готовься к кратному увеличению и сроков, и бюджета.
-
Переходи на ЭДО возня с физическими бумажками отожрёт до 30% от срока согласований, и это практически на пустом месте.
Внесение правок
Ну и второй важный вопрос внесение правок, которые могут запросто сломать всю предыдущую работу и поставить перед фактом Вам придётся начать всё заново.
Но это нормально, мы, в конце концов, все с вами делаем новые штуки, тут проложенных рельсов нет ни у кого.
Часы на внесение правок: непрогнозируемо. Иногда правки незначительны, иногда работу приходится просто переделывать.
Разные подрядчики разные чеки
А теперь, собственно про деньги.
Одну и ту же работу можно сделать разными исполнителями, я даже как-то это описывал вот тут, но слушать больно звук писался из зала, простите. Суть в следующем выбирайте подрядчика в зависимости от своих процессов и желаемой степени контроля и погружения в ваш проект.
Вот разные типы подрядчиков, которые могут разработать для вас корпус. У каждого есть достоинства, недостатки и, условно, средний чек нормо-часа:

Т.е. если бы ваш проект делал свой сотрудник, то он бы, допустим, сделал его за 175К и примерно 2 месяца работы фуллтайм, т.е. 8 часов в день, прям плотнячком. Фрилансер за 350К, студия за 500К, а бюро за 700К.
И, конечно, вывод однозначен:
Если результат одинаков, зачем платить больше?
Но так не работает, такие дела. Штука именно в издержках, возникающих в процессе разработки штатный сотрудник не сможет и нарисовать все хорошо, и сделать документацию, и все согласовать с заводом (который сам же и должен найти). Для одного проекта таких сотрудников надо уже 3 человека если по-хорошему.
Фрилансер может уже больше, но там есть тайланд-головного-мозга другие риски. И, опять же, всем, что связано с прототипами (не макетиками на 3D-принтере, а когда все серьезно), вы будете заниматься сами.
Бюро тоже не ангел все сделаем за вас, но и возьмем больше всего денег.
Еще важный момент профессионализм, т.е. количество ошибок и проблем. Штатного сотрудника ты знаешь, знаешь, что он может, а чего нет. Можно предположить, где он ошибется (кстати, вот тут чуваки влетели на 12М из-за ошибки штатного конструктора formlab.ru/12mln-v-minus).
С фрилансером всё не так прозрачно по сути, ты просто веришь в него. Чем выше уровень подрядчика (квалификация, число реализованных проектов, количество спецов в компании и пр.), тем лучше качество услуги, что логично суммарный опыт внутри бюро или студии больше, чем у одного человека. Но и сумма чека за этот опыт тоже увеличивается.
В конечном итоге всё сводится к очень простому вопросу: кого выбрать?
Если ты считаешь свое время самым дорогим и тебе нужно добежать до продаж продукта максимально быстро и не рискуя, то платишь бюро.
Если хочется всем рулить, т.е. тратить на задачи свое время, а срок выхода на продажи не давит обращай внимание на левую часть таблички, где чек будет минимальным. Так можно сэкономить. Подробнее про экономию ниже.
Экономим как?
В разработке всегда есть такая штука, как коммуникативные издержки. Под этим словосочетанием я подразумеваю весь комплекс коммуникаций с заказчиком. Но самое фантастическое заключается в том, что стоимость издержек может быть равна стоимости работы над проектом. Наглядный пример: на фактическую работу, условно, ушло 3 недели, на обсуждения и согласования год.

И тут ты:
-
либо берешь коммуникации на себя, т.е. занимаешься проектом полностью, по сути, оплачивая несвязанность разработчиков (электроника, дизайн, инжиниринг, производство);
-
либо перекладываешь все это на специальных людей, но тогда платишь им за это + за профессионализм разработчиков (опытный специалист делает меньше ошибок), т.е. либо ты готов рисковать и работать на веру, либо хочешь подстелить, потому что важно быстрее выйти на производство и начать уже продавать свой продукт.
Первый путь это про экономию, второй про скорость выхода на продажи.
Примеры
Ну и слайды-слайды примеры с цифрами:
Компактный корпус 200 000 ($ 3000) https://formlab.ru/portfolio/vk7

Компактный герметичный корпус 350 000 ($ 5000) https://formlab.ru/portfolio/vk

Корпус в стойку 450 000 ($ 6500) https://formlab.ru/portfolio/case19

Настенный многофункциональный корпус 500 000 ($ 7000) https://formlab.ru/alarm_system_pritok

Корпус светильника 600 000 ($ 8500) https://formlab.ru/portfolio/dragonfly

Настольный корпус 600 000 ($ 8500) https://formlab.ru/helium_leak_detector

Носимый сложный корпус 700 000 ($ 10 000) http://old.formlab.ru/promyishlennyiy-4g-modem-dlya-televizionshhikov-mobile-4g-router/

Носимый сложный корпус 800 000 ($ 11 500) https://formlab.ru/analyzer

Носимый сложный корпус 1 000 000 ($15 000) https://formlab.ru/luch

Напольный сложный корпус 1 200 000 ($ 17 000) https://formlab.ru/gamma_complex

Напольный сложный корпус 1 700 000 ($ 25 000) https://formlab.ru/bankomat_sberbank

Кабина станка 3 000 000 ($ 45 000) https://formlab.ru/mclt_2

Ценники усредненные, плюс дополнительно суммы даны в долларах (на 4 августа 2020 года): просто оценить порядок бюджета.
Выводы
Цель заметки, как я уже писал, показать, как появляется формируется цена в разработке корпуса, точнее, как это делаем мы в Формлабе, и сколько в итоге придётся потратить на корпус.
Вы уже знаете, из каких этапов состоит работа и понимаете, сколько человеко-часов придётся на всё потратить. Кроме прочего, у вас уже есть табличка с примерными расценками каждого специалиста.
Вывод банальнее некуда: правильная разработка не может стоить. Ну, вы поняли.
Но, к счастью, и способы сэкономить тоже имеются.
Что ещё почитать по теме:
Где выгоднее производить
корпуса в Китае или России? Мы сравнили, пользуйтесь
Макет, прототип, серийный
образец и вот это всё учим термины
Российское приборостроение:
вертели мы ваш дизайн на пальцах
Как спроектировать корпус для
прибора. Полное руководство
Как не промахнуться с
бюджетом на серийное производство корпусов: 20 примеров из практики
бюро по инженерному дизайну
Как не промахнуться с
бюджетом на серийное производство корпусов-2: цены на мелкосерийное
литьё пластика
Правильно готовим прототип.
Технологии прототипирования корпуса
Как за пару минут
самостоятельно рассчитать цену корпуса устройства
Промышленный дизайн для
бизнеса: минимизируем издержки, экономим на ненужном, вкладываем в
главное
Промышленный дизайн для
бизнеса, часть 2: дизайн вместо маркетинга или делаем продукт,
который продаст себя сам
UPD: чтобы 2 раза не вставать скоро выходит вторая часть нашего гайда, с обновлением статей и новыми материалами. Кому хочется обновлений, велкам сюда: formlab.ru/habr.